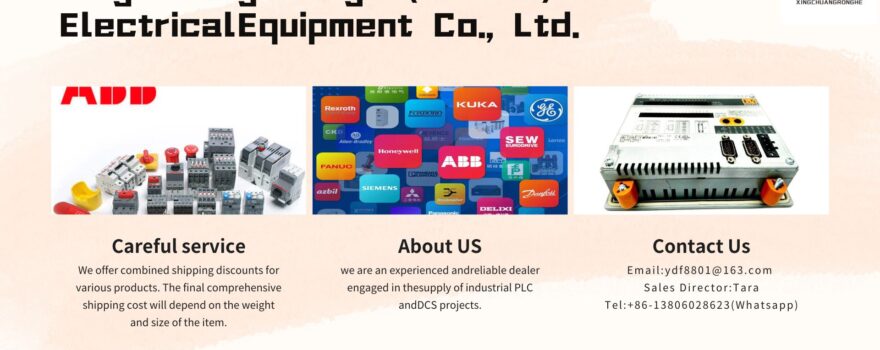
When an alarm blared at 6 a.m. in a Shanghai waste-to-energy plant—signaling critical furnace overheating—an AI vision system took autonomous action. Within minutes, it stabilized combustion by auto-adjusting fuel and airflow. This intelligent control solution, co-developed by Schneider Electric and partners, integrates machine vision with real-time optimization algorithms for precision industrial automation.
“AI industrialization has entered an ecosystem-driven era,” declared Yi Xiong, SVP of Schneider Electric China. “Isolated technologies cannot bridge the industrialization gap when AI moves from labs to boiler rooms.” He framed scaling as a triple relay race:
-
Technology Integration: Full-stack capabilities require collaboration. For example, their waste-plant AI merges computer vision, optimization algorithms, and control systems—beyond any single company’s scope.
-
Scenario Expertise: Lacking mechanical insight, even advanced algorithms fail. In a wind-turbine project, 20 years of vibration analysis from partners enabled accurate bearing-failure models.
-
Scaling Networks: Replicating pilot successes demands open platforms. Schneider’s “Go Green” initiative has scaled an AI quality-inspection solution from its Wuxi factory to 12 manufacturers.
Three Engines for Ecosystem Competitiveness
Schneider’s ecosystem strategy rests on:
-
Open Culture: Internal “Impact” values break silos. In 2024, logistics teams shared predictive delay models with production units.
-
Technical Leadership: 200% AI patent growth in three years; 99.2% accuracy in industrial visual recognition anchors partnerships.
-
Hybrid Talent: “Digital Citizen” program trains engineers mastering both Modbus protocols and Python. 500 OT-AI experts will be certified by 2025.
Ecosystem in Motion
Vertical Depth:
-
“Go Green” with MIIT yielded 40+ co-innovations, including an AI energy optimizer cutting power use by 12% at 30 plants.
-
Joint lab with NVIDIA developed smart cabinets reducing GPU cluster energy by 15%.
Horizontal Expansion:
-
World’s first hydrogen-equipment digital twin with Zhejiang Hydrogen Center slashes electrolyzer fault-response time by 90%.
-
Open-source knowledge graphs help SMEs reduce manual data labeling by 80%.
Tangible outcomes include two “Lighthouse Factories”: Wuxi boosted product yield to 99.98% via AI process optimization, while Shanghai improved logistics efficiency by 40%. Concurrently, the “AI for GREEN” report warns that computing power’s energy demands require industry-wide collaboration.
“Ecosystem synergy is a marathon,” Xiong concluded. At WAIC 2025 (July 26), Schneider will unveil an industrial AI “toolkit” co-created with partners, spanning predictive maintenance and energy optimization across 20 scenarios. “Passing the ecosystem baton is key to winning the last mile of AI industrialization.”